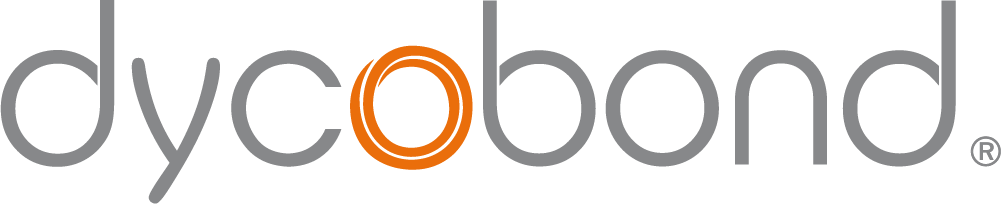
Also for large size molds
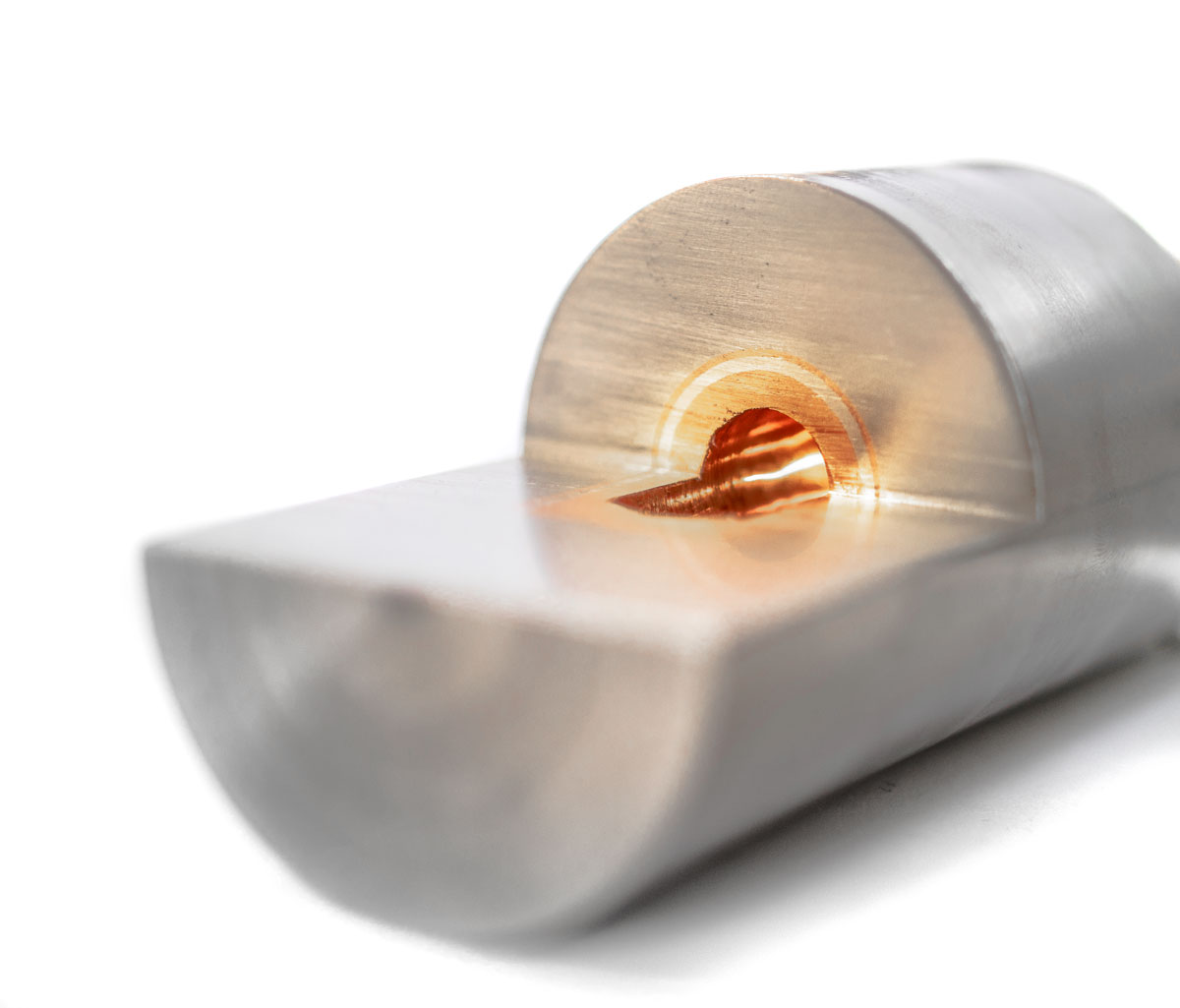
The Dycobond® process revolutionizes internal mold cooling by inserting a thick, multilayer lining into the cooling channel done a single working step directly during the hardening process.
In the EU and US patented process, the lining diffusely joins the steel to ensure an optimum heat transfer. A stainless steel barrier layer located inside the copper lining also prevents water from escaping from the cooling channel.
Advantages
- Significantly higher cooling performance
- Efficient protection against leakage
- Improved mold durability
- Uninterrupted casting in series casting processes
- Less downtime
- Short casting cycles
- Higher casting quality
- Lower energy consumption
- Environmentally friendly
- Cost saving
Technology
The thick copper lining of the cooling channel doubles its cooling surface (connecting surface between steel and copper) and thus also its cooling effect. If the distance between cooling channel and mold cavity is reduced by fifty per cent, this will again double the cooling effect. Dycobond® also improves the homogeneity of the temperature distribution in the shape contour.
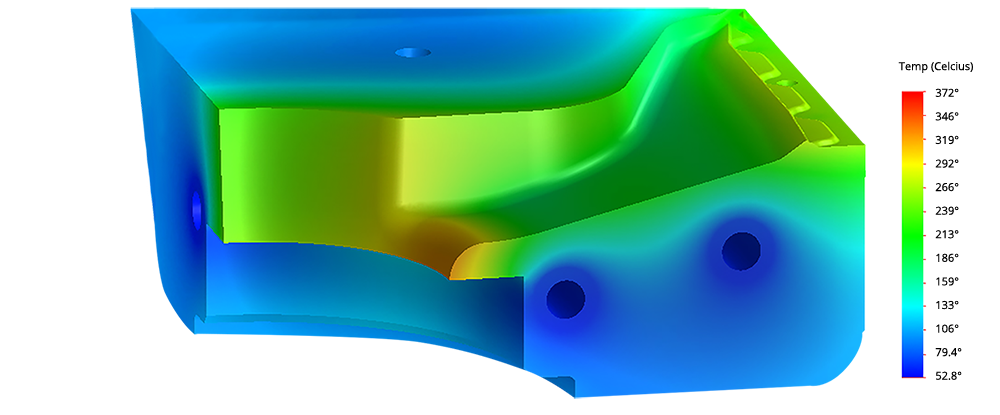
The Dycobond® design includes a resilient stainless steel barrier layer embedded in the soft copper. If, due to the high stress loads of the casting operation, hairline cracks form in the hardened mold steel, they are absorbed by the outer copper mantle when penetrating the cooling area and then stopped by the stainless steel barrier layer. As a result, the high crack-sensitivity of the chromium-alloyed steel poses less of a problem and the cooling channels may be situated much closer to the mold cavity without risk.
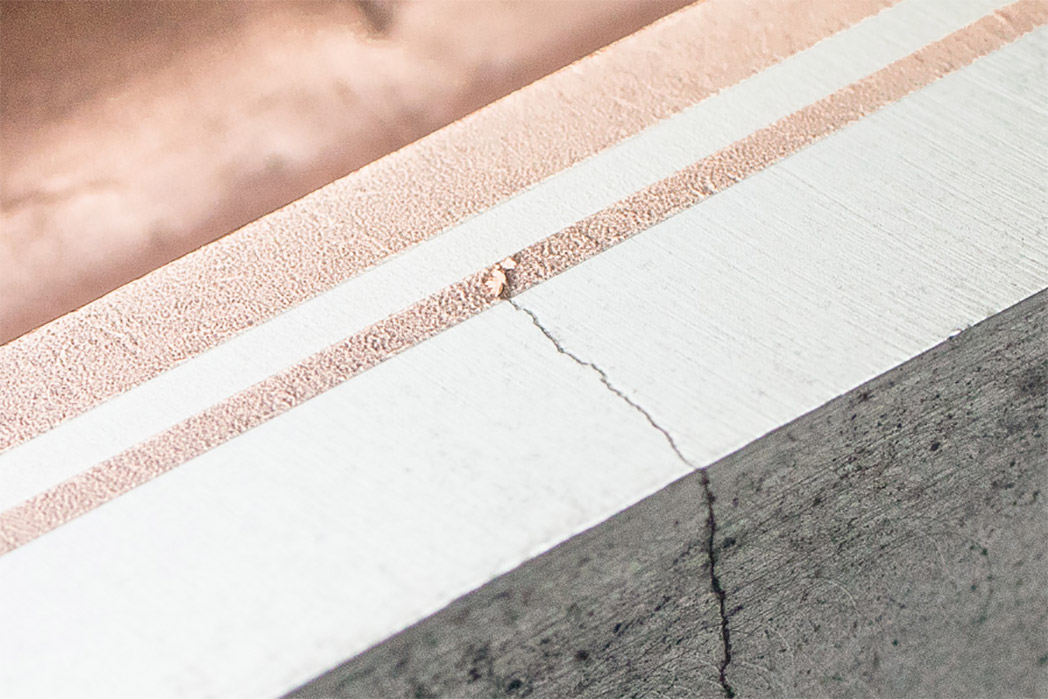
The high-quality, diffusive connection between steel and copper is the prerequisite for our cooling efficiency and also for the tightness of the cooling channels.
The Dycobond® technology makes it possible to produce a spatial composite of materials with different thermal expansion properties. The result is an excellent, high-strength and sealed diffusion bond.
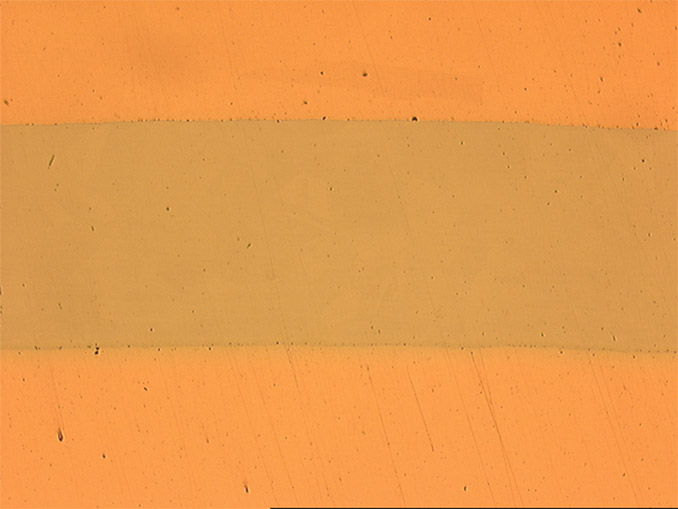
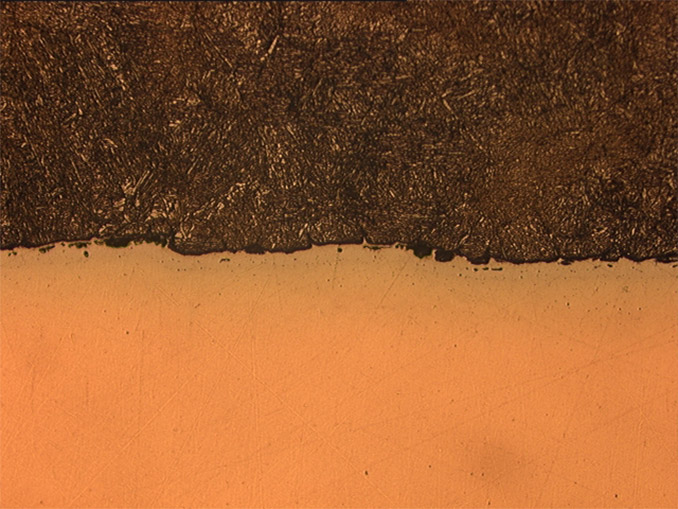
Production
Once relevant cooling channel areas are designed, an enlarged bore (diameter 25.2 mm or larger) is prepared and the mold insert is sent to Dycobond GmbH or to the licensed hardening shop.
There the copper and stainless steel interior parts are inserted. In the next step, the Dycobond® hardening takes place in a vacuum oven. In the final step, the mold manufacturer then drills the cooling hole (diameter 10-15 mm) into the copper core.
Applications
Whether dies, die inserts, slides or die cores, Dycobond® offers new possibilities wherever cooling capacity through mold cooling is to be increased. Mold size is unlimited. Since a short production cycle has a high priority, cooling improvement of the mold gates brings about significant benefits. The result is a reduction or elimination of the secondary spray cooling – often by up to 20, 30 or even 40 seconds. A prime example is the sprue plate, into which the mostly large-area and also thick-walled pouring run is embedded. Another application example for more efficient circulating cooling is an elongated and thick-walled pouring run along the die cavity.
The Dycobond® design is suitable for both recirculating line cooling and fountain cooling. One example of a fountain cooling system is the large internal die insert for gearboxes and clutch housings or the bearing area in crankcase molds. Also noteworthy is the conical central spur (anvil) in triple plate tools for the production of large structural parts.
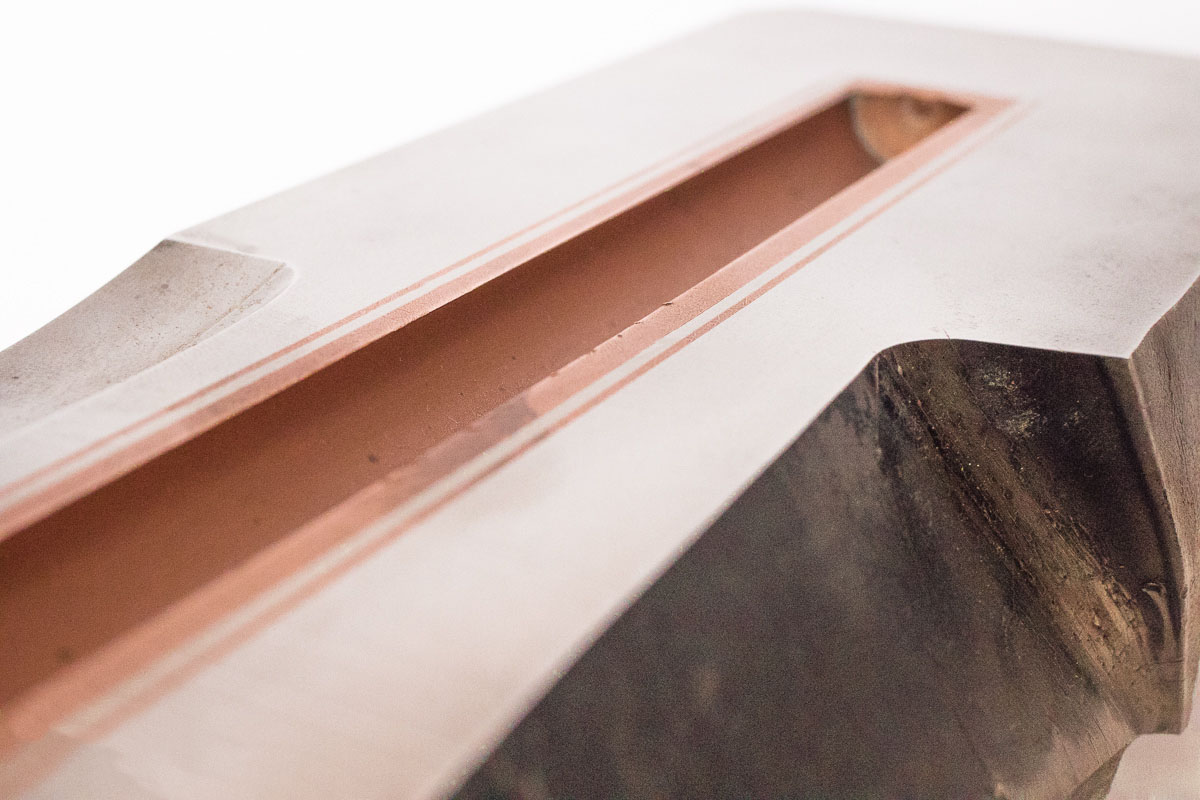
In permanent mold casting, variothermal cooling (swelling cooling) is increasingly used for optimizing the structure of the casting. With Dycobond® the distance of the cooling to the mold cavity can be reduced, which considerably increases the efficiency of a swell cooling. Such applications would be, for example, cylindrical cores for engine blocks, domes inserts for cylinder heads and contour cores for chassis parts.
Cooling efficiency, protection against leaks and homogeneity of the heat balance are very important for large-scale dies. In places inaccessible to cooling, copper inserts can also be used as thermal conductors without an internal water cooling.
Contact us!
Dycobond GmbH
Saarner Str. 433
45478 Mülheim a. d. Ruhr
Contact:
Dr.-Ing. Gerhard Betz
Tel. +49 (0) 208 589 435
Licensed partner for large size mold parts: VTN Witten GmbH, Rüsbergstr. 75, 58456 Witten, www.ihi-vtn.com
For more applications of SteelCopper CompositeCooling you could also be interested in the Mecobond® technology: www.mecobond.de
Reading tips (mostly german):
GIESSEREI PRAXIS Article „Druckguss für die Elektromobilität“
GIESSEREI PRAXIS Article about the StahlKupferVerbund-Form
GIESSEREI PRAXIS Article about Aluminiumdruckguss mit Zentralanguss (Dreiplattentechnik)
GIESSEREI PRAXIS Article „Werkstoffverbund verhindert Wassereinbruch in die Form“
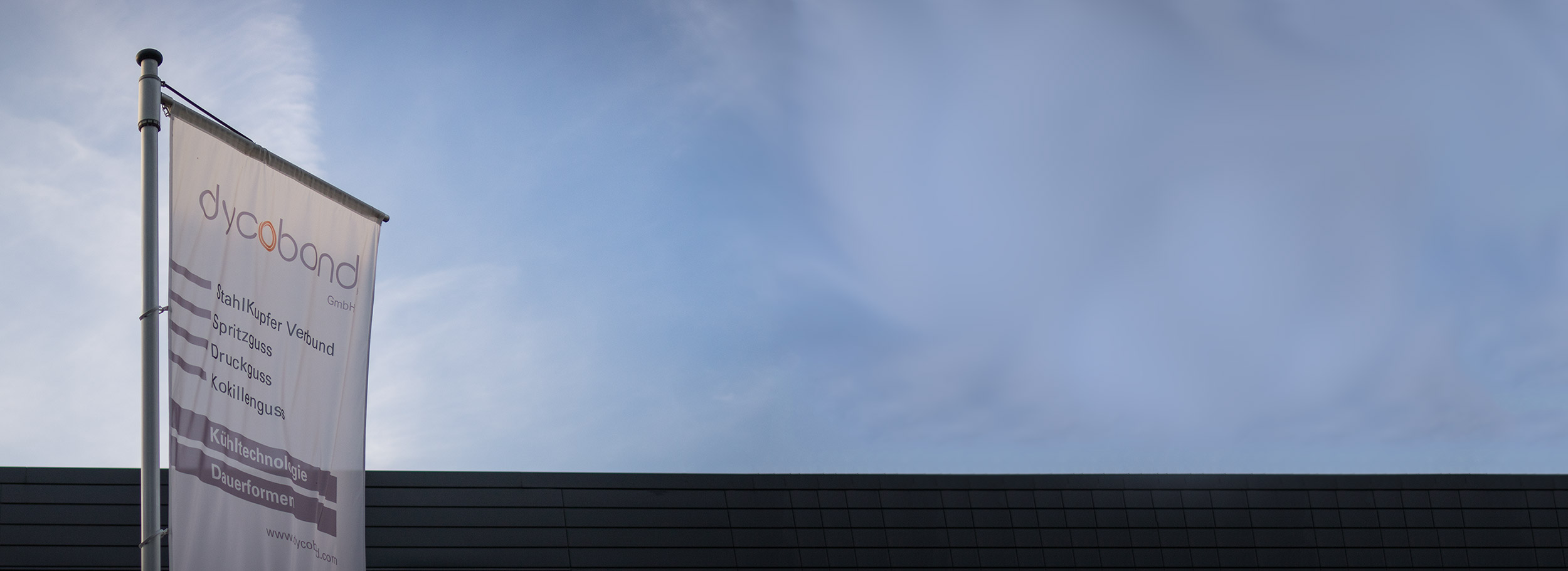
Dycobond GmbH | Saarner Str. 433 | 45478 Mülheim a. d. Ruhr
Legal info & privacy policy | Design & Programming: Rolf Krüger Design